Second-generation broommaker reveals his meticulous process
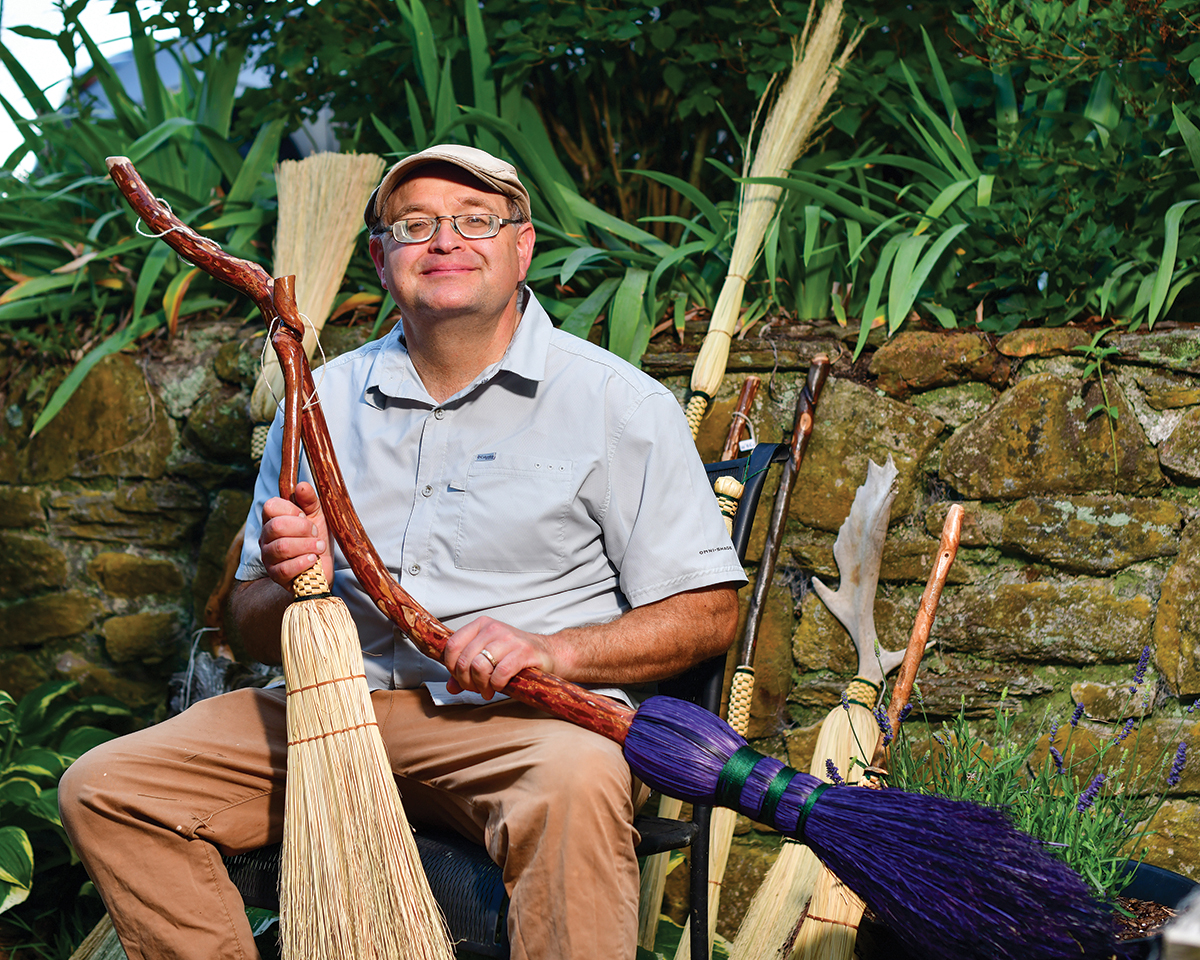
Images used courtesy of Diana Gates Photography
There’s an old Appalachian housewarming tradition that involves three gifts to be given to a newlywed couple setting up in a new home – bread, salt, and a broom. Bread signified that the house would never know hunger; the salt, sprinkled on the floor, promised the couple’s life together would have flavor; and the broom was to sweep the salt out the door along with any evil spirits, to whom salt was irresistible.
Marlow Gates would be happy to supply the broom for the ceremony. He’s been hand crafting traditional brooms for decades as a second-generation crafter, following in his late father Ralph’s footsteps as the guiding spirit of Friendswood Brooms, based in a 150-year-old former general store in Big Sandy Mush, just outside Leicester in the far northwest corner of Buncombe County.
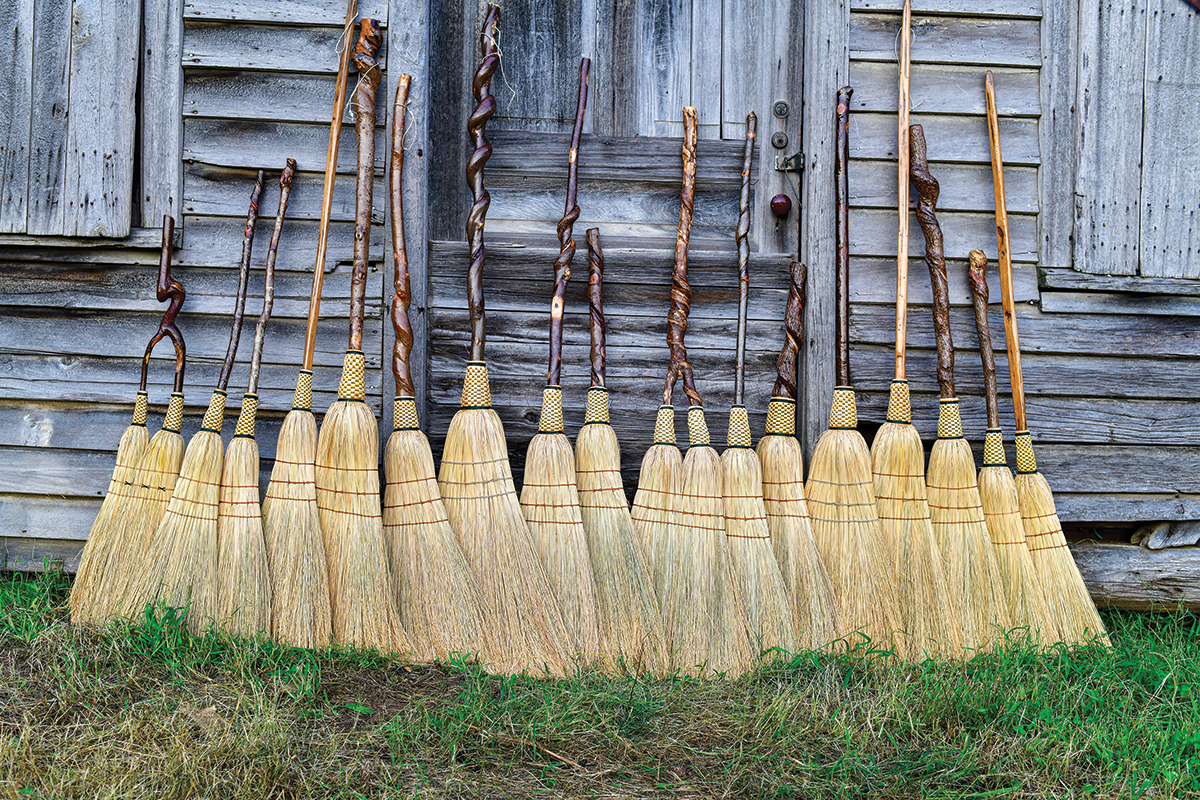
“I grew up making brooms after school and helping Dad and my siblings out in the shop,” says Gates, who made his first broom when he was five years old. After earning a degree in industrial design from North Carolina State University, Gates began working alongside his father and helped grow the business, which today produces both brooms for everyday use and a line of sculptural pieces prized for their beauty and creative design.
One of Gates’ earliest memories is of the bare winter woods, where his father would take him along on the hunt for suitable broom-handle material. “He taught me to look for wood that had had vines attached to it,” Gates recalls, “because the vines would leave marks on the wood that you could incorporate into the handles. Gathering wood in the winter is one of my favorite parts of making brooms.”
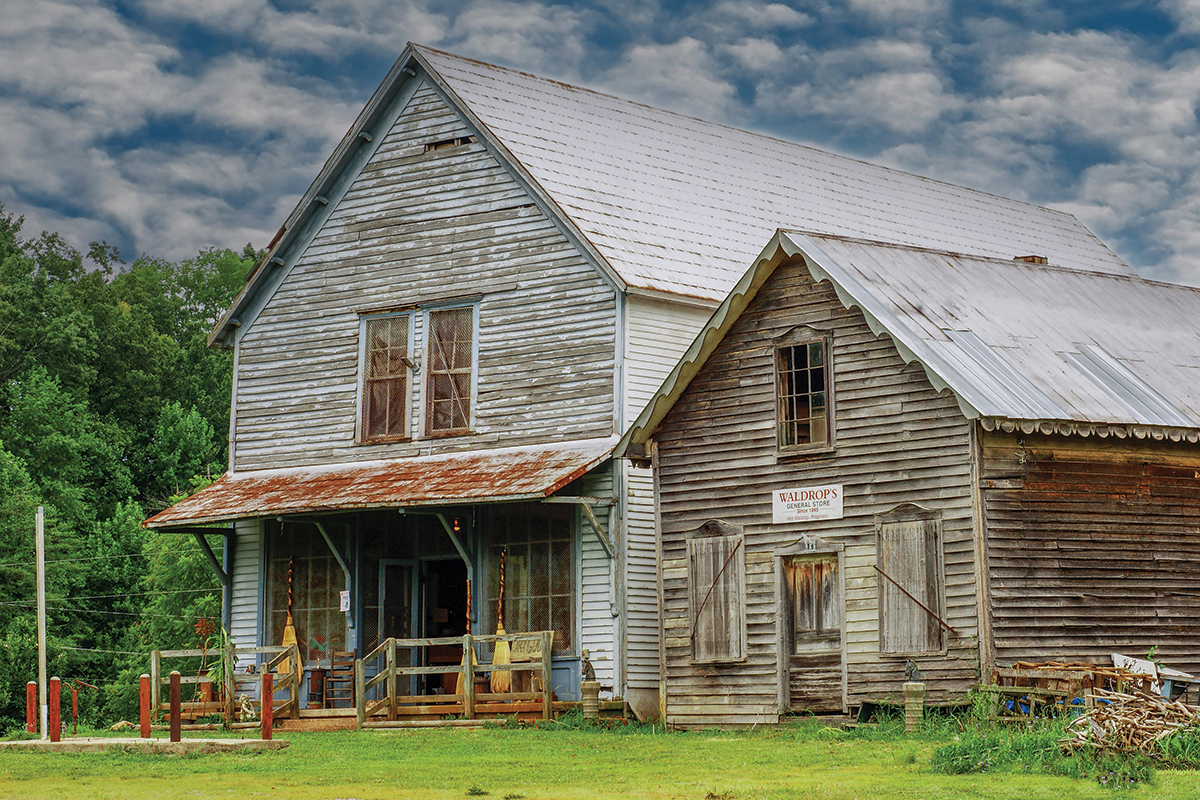
Brooms have also brought romance. When Gates was demonstrating broom making at Mast General Store in Waynesville 26 years ago, he was watched with interest by the general manager of the Candy Barrel next door. That was Diana, now a veteran broom maker herself, specializing in carving and sanding the wooden handles. “She watched me working and said she thought she could do that,” Gates recalls, “so I taught her to weave her first Cobweb broom that day.” The couple married in 1997.
While most of Friendswood’s brooms are meant to be used for sweeping, Gates estimates that 25 percent of the company’s output are sculptural pieces, “never meant to touch the floor,” as he points out, that he and Diana design together. But all their brooms incorporate straw derived from broomcorn, a type of sorghum, as much as a ton of it used each year; hand-carved and sanded handles made from native wood; and centuries-old threading techniques Gates learned from his father. And unlike mass-produced brooms bound with wire, Friendswood’s brooms come with a lifetime guarantee and can be “re-broomed” for a modest fee. “We get two or three a month that come back to be re-broomed,” Gates estimates. “And they’ve already been in use for up to 30 years.”
After years of traveling to exhibitions and craft fairs, Gates is happy to have settled down with a permanent exhibition space at Biltmore Farms, as well as crafting brooms at Friendswood’s mountain studio. “Each of our brooms is unique,” Gates says.
“They incorporate traditional Appalachian strength and longevity.”
Friendswood Brooms, 8 Willow Creek Road, Leicester, 828-683-9521, friendswoodbrooms.com. The studio is a stop on the Come to Leicester Annual Artist Studio Tour happening Saturday, Aug. 19 and Sunday, Aug. 20, 10am-5pm, cometoleicester.org. Gates also crafts brooms in the barn at Biltmore Estate’s Antler Hill Village (biltmore.com).