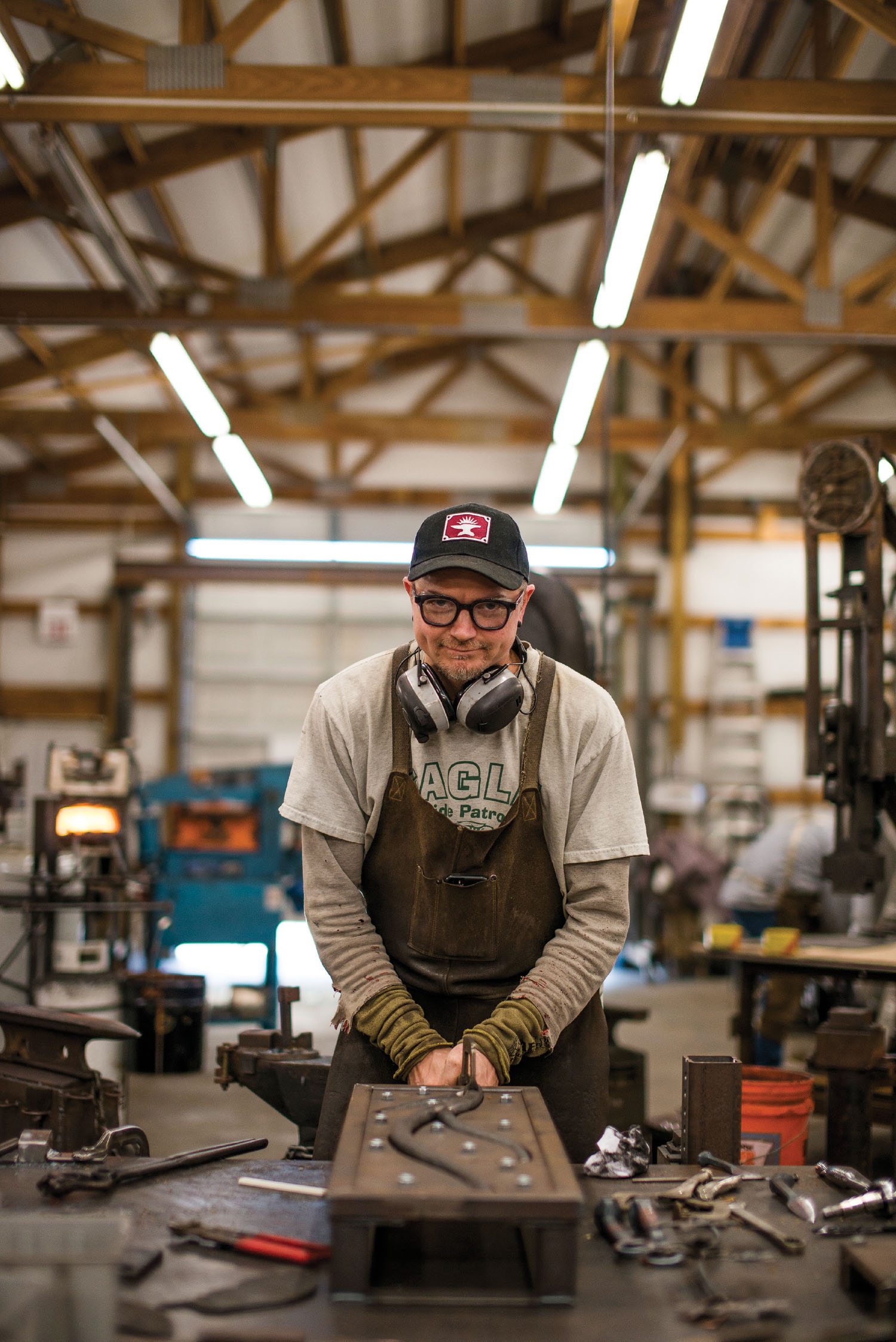
Portrait by Karin Strickland
It’s a fitting career trajectory for a blacksmith: Matthew Waldrop forged his company, Northern Crescent Iron, the hard way. Success was followed by setbacks, multi-state moves, and start-overs. Until 2007, NCI was strictly a two-man operation. Waldrop had enough demand for his decorative and architectural ironwork that he’d taken on a full-time operations manager, Jeremy Duke, who’s still with the company after 11 years.
But then came the 2008 recession. “It was really hard on us,” Waldrop says. The company almost collapsed, so, he says, “we started putting cabinet hardware, bottle openers, knives and [other items] on ETSY, and it just kind of took off. It was largely accidental and it just kind of grew on its own.”
Now, NCI has its own website and online store, along with four employees who handcraft an inventory that ranges from small accessories such as keychains to original designs for home décor and complex, large-scale architectural projects. The business has been housed since 2013 in Flat Rock.
It’s a far cry from Waldrop’s first years blacksmithing in his native Michigan, apprenticing with an armorer who made replica swords, shields, and full suits. The artist grew up in Detroit but his family tree resides deep in Western North Carolina. “I have very old roots here with the Waldrop family,” he says, “and I feel more at home in the South.” He was drawn to the area in the early 1990s, living in Asheville for several years before traveling to learn his craft as far away as New Mexico, where Northern Crescent Iron first came into being.
He’d been working at a small blacksmithing forge just outside of Taos, but the hours became inconsistent, and sometimes nonexistent, at a time when Waldrop had a partner and two children to support. “I had to take a huge leap of faith and started working solo,” he says of his decision to set himself up under the NCI banner. But after three years, the pressure and stress became too great. He shut the company down and moved back to Asheville, where, a year later, he reopened Northern Crescent in the Phil Mechanic studio complex.
Online sales of its smaller items kept the company going after the 2008 crash, but another boost was the partnership Waldrop formed with Darren Green’s The Old Wood Co. “Darren approached me to make some furniture that he was having trouble getting made,” Waldrop recalls. “We started working together and I made the first ‘Life’ tree table and brought it to him as a prototype. He bought it, and we’ve been making those for him ever since.” Fashioned from Old Wood’s reclaimed, recycled lumber and Northern Crescent’s hand-wrought iron framing and pedestals, the Life brand, designed to resemble trees, has been joined by two new series featuring side tables, chairs, and stools.
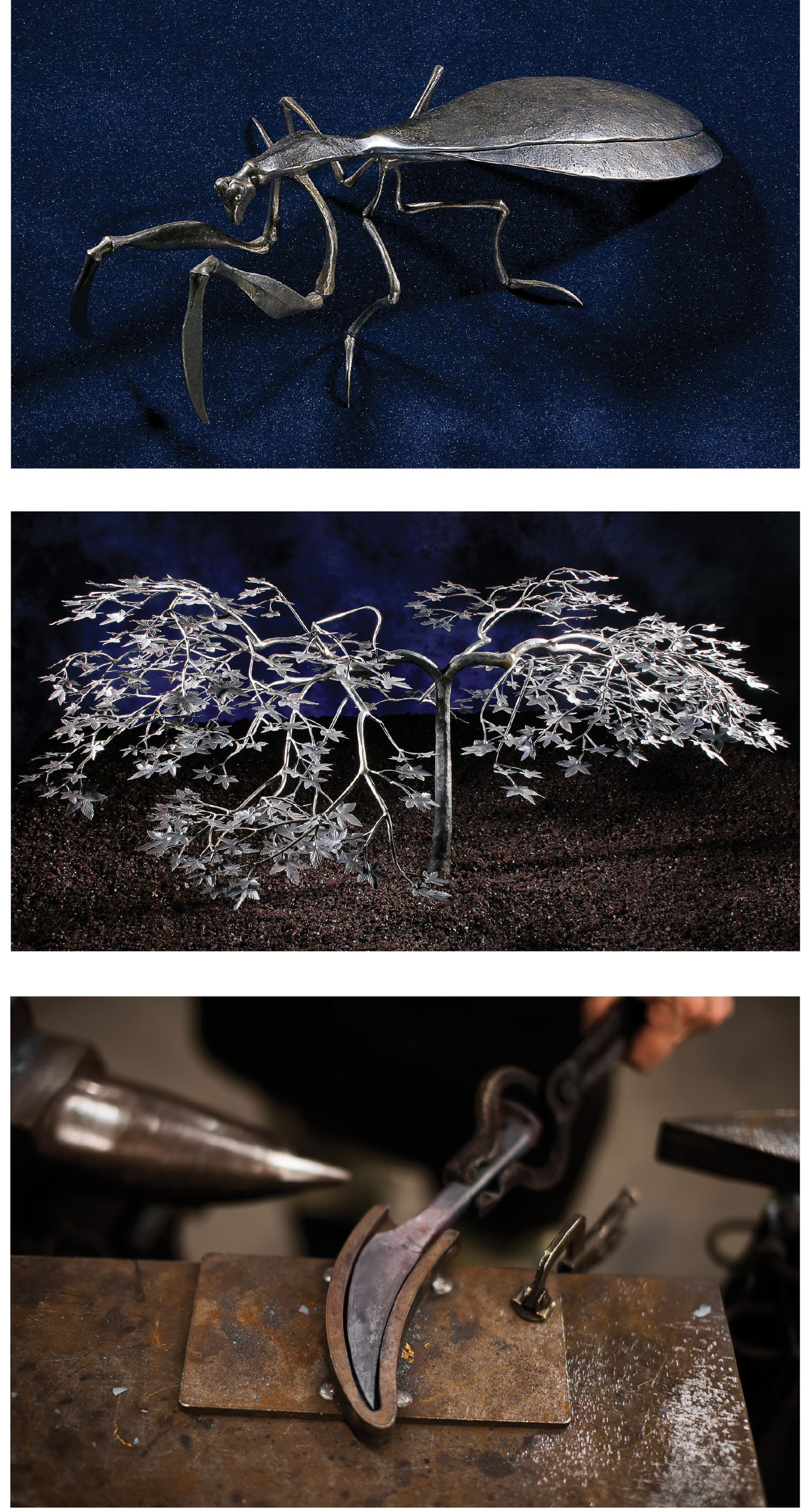
“They’re my sole original designs that we make only for Old Wood,” he explains. “It’s all forged pipe, and that can be hard to work, but it needs to be light. That’s why we use the pipe. There’s a lot of welding and finishing.”
In the artist’s intricately wrought piece “Japanese Maple,” each of dozens of hand-formed, veined leaves is invisibly welded to its branch. His sculpture line also includes a butterfly garden so carefully finished it seems to tremble with the fluttering of wings, and a watchful praying mantis balanced on six slender legs.
Challenges on a larger scale come with NCI’s architectural fencing, gates, and stairway railings derived from natural forms. “All big luxury-home projects are complicated,” admits Waldrop. “The key is to simplify them when you can so everyone is happy. And don’t overthink it.”
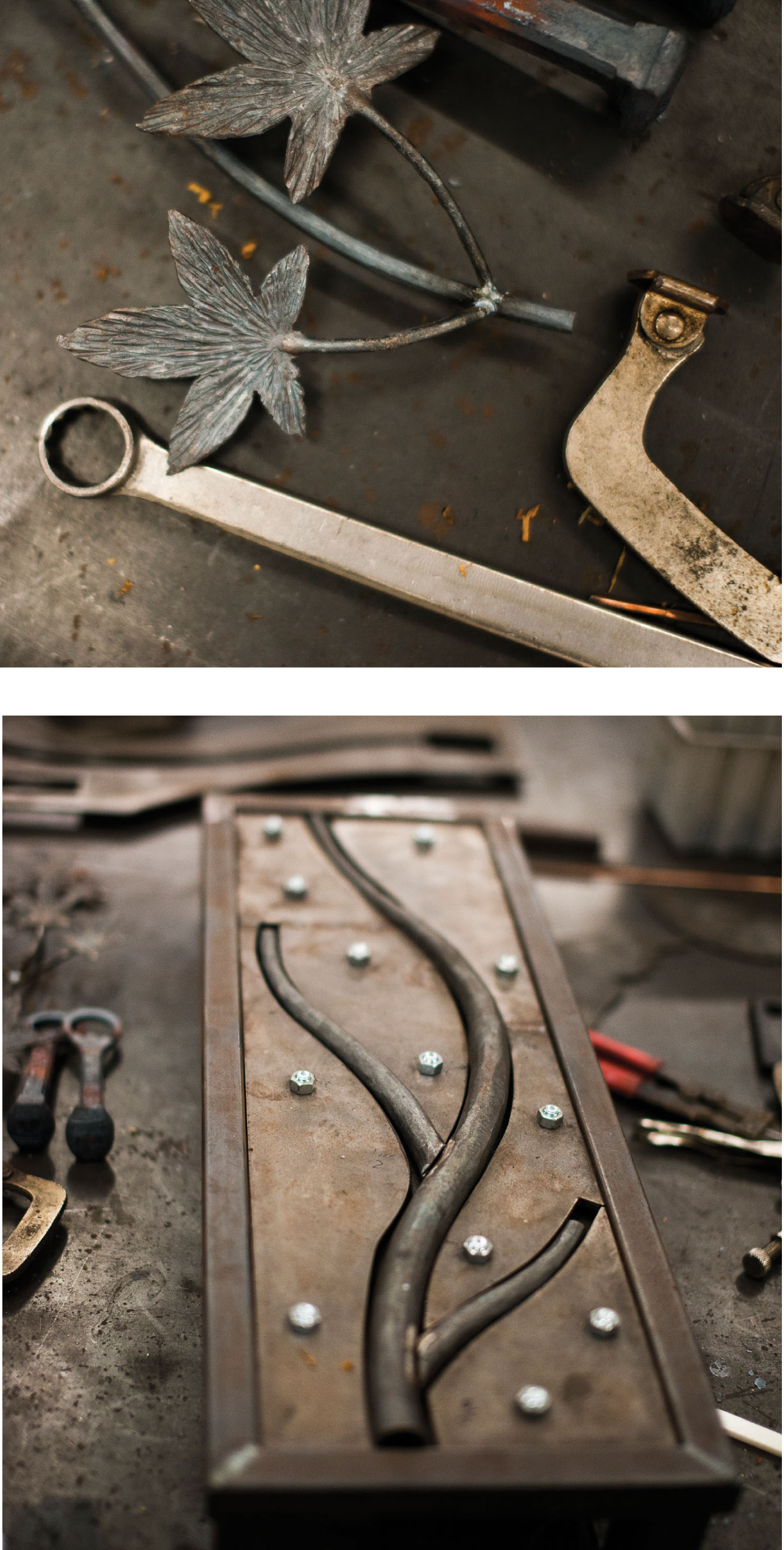
Photos by Karin Strickland
Northern Crescent Iron, 16 Kay Road, Flat Rock, northerncrescentiron.com or nc-iron.com. Visitors are welcome during regular business hours (Monday-Friday, 9am-5pm). Many smaller items are for sale on the site’s shopping page. Call 828-848-8884 or e-mail info@northerncrescentiron.com for more information.