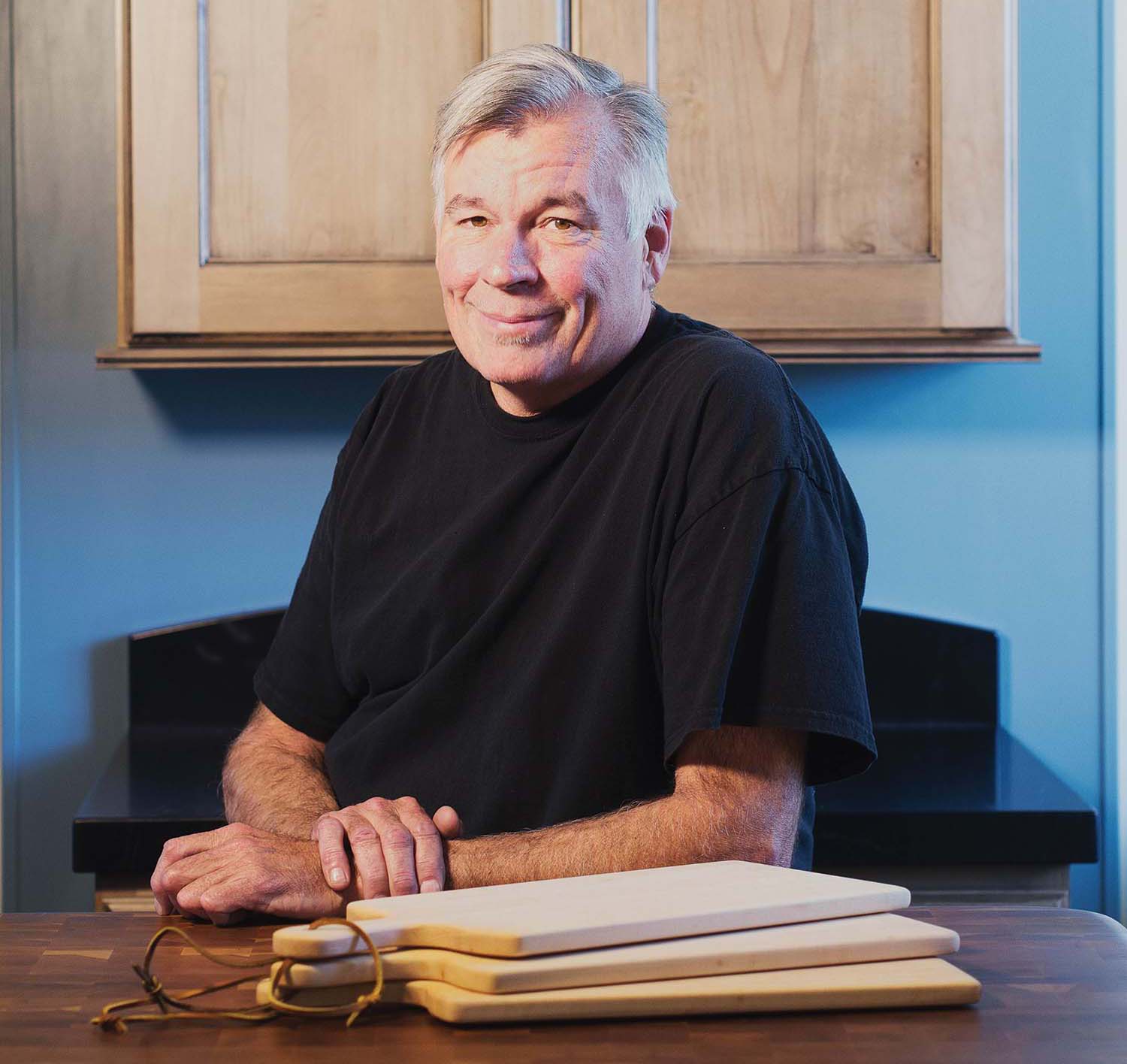
One might think Sam Benbow deserves a break from wood. At his regular gig, he works as a kitchen and bath contractor, creating custom hardwood cabinetry for clients throughout Western North Carolina. When the day is done, he crafts cutting boards from the scraps of those projects.
But Benbow says making cutting boards is just the kind of break he needs. “It’s almost like therapy, as opposed to contracting,” he explains. “You have no client, no timetable, no dimensions you have to stick to — you can make whatever you want.”
Benbow started producing cutting boards to give away as gifts for friends and relatives. “We had lots of hardwood pieces left over from doing work at the shop, so after having them just pile up for years, I figured I’d start recycling them,” he recalls.
All of the recipients loved his work, so when he and his son wanted to raise some money for a family vacation, they figured the boards would sell at seasonal markets and craft shows (they set up regularly at the North Asheville Tailgate Market). “The trip never materialized, but we kept making cutting boards,” says Benbow.
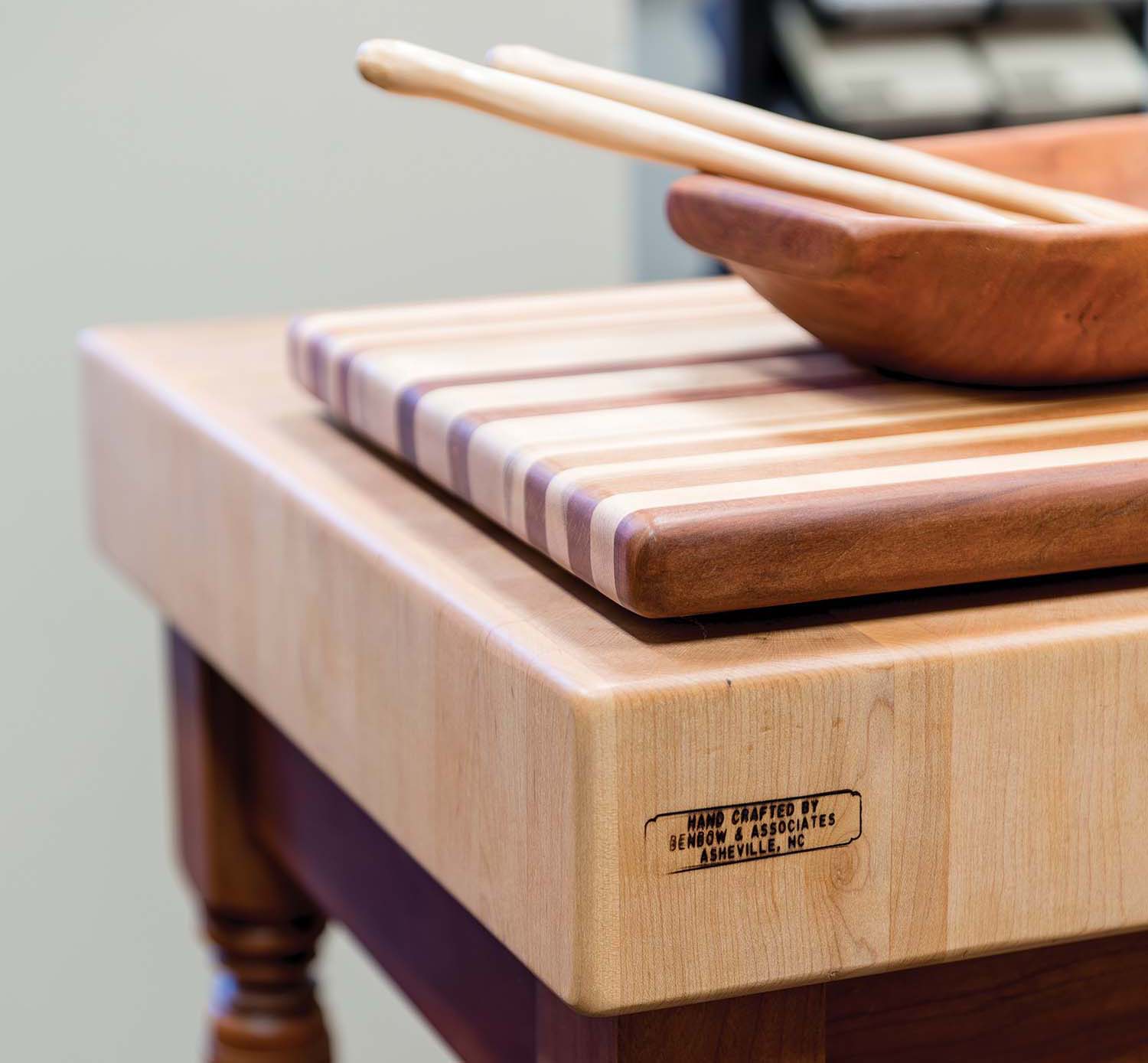
Currently, he sells his cutting boards through his showroom in the River Arts District, as well as wholesale to clients who want to give the boards as gifts themselves. He also participates as an exhibitor at Western Carolina University’s Mountain Heritage Day.
The different types of boards Benbow makes are defined by how their woods are cut. Face-grain boards are made with lumber from long slats running up and down the tree trunk; the softest type, these boards are best for serving trays or display platters. Their thin, carefully arranged strips give the impression of a flag, the banner for some multicolored army of trees.
In contrast, end-grain boards are made with cuts of lumber from across the trunk. These boards make sturdier chopping blocks because the wood fibers face the knife as they were arranged in the tree. “That’s how the old butcher blocks were made years ago,” Benbow explains. “It basically takes two cutting boards to make one end-grain board: you’re surfacing them flat, sawing them into strips, then gluing them back together so your grain runs vertically.”
All of Benbow’s materials come from area distributors such as Asheville’s Gennett Lumber Co. and are mainly sourced from local domestic hardwoods, although he occasionally draws on unique imported materials such as mahogany-like sapele. He favors cherry and walnut for their rich colors, as well as oak and maple for their durability.
Those sturdy woods mean that one of Benbow’s boards can last for a lifetime — and beyond. “When I do shows, people come up and tell me stories about cutting boards they inherited from their father or grandfather,” he says. “I’ve made boards for 30 years now, and some of mine are just now starting to get passed down.”
Benbow & Associates, 372 Depot Street, Suite 34, Asheville. For details, call 828-281-2700 or visit benbowassociates.co.